From the 2008 Tesla Roadster to today’s incredible feats of engineering rolling out of gigafactories around the world, manufacturers have made significant strides to make EVs affordable to the masses.
The original Tesla used cylindrical 18650 NCA batteries from Panasonic, because they were commercially available and inexpensive. Tesla progressed to the Model S and X with the same 18650 form factor, but engineering improvements improved battery range. The Model 3 now uses 21700 cylindrical cells exclusively, allowing higher energy density, and in turn even longer range. Tesla is not the only one making advancements. Other large automobile manufacturers are also pushing to increase battery energy density and drive down the cost of EVs.
As different active material chemistries are becoming more cost competitive it has introduced some unique ideas for the future. Lithium iron phosphate chemistry for example has been used in EV buses in China because of its stability and ability to be charged and discharged at faster rates than NCA/NMC. The size of a bus allows for larger battery modules to make up for the lower per cell capacity, therefore making it economically viable. EV manufacturers main focus was on squeezing out as much energy from NMC chemistries, but statistics were recently released showing large improvements in LFP energy density per a tweet by @DKurac.
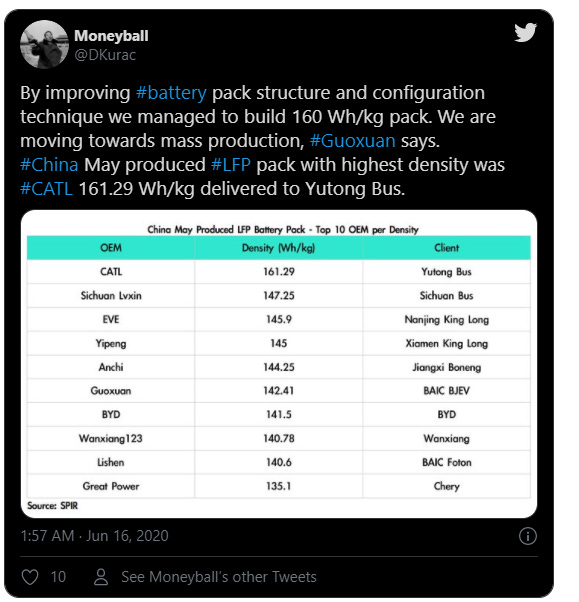
This data suggests that the top three producers can make battery packs of approximately 151 Wh/kg. Meanwhile, just 6 days earlier the same Twitter account posted energy densities of various NMC batteries. The average of the top 3 is 268 Wh/kg.
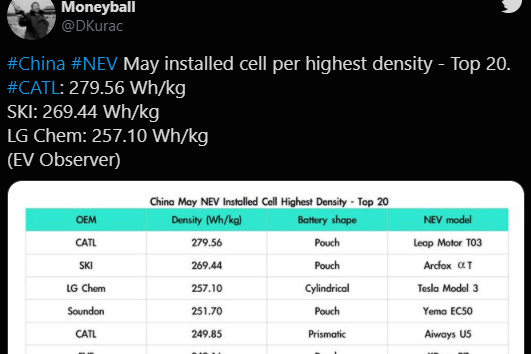
It is particularly amazing to see how far LFP has come on the chemistry and engineering fronts. In the below table I have compared specific energy improvements based on 2017 data(1).
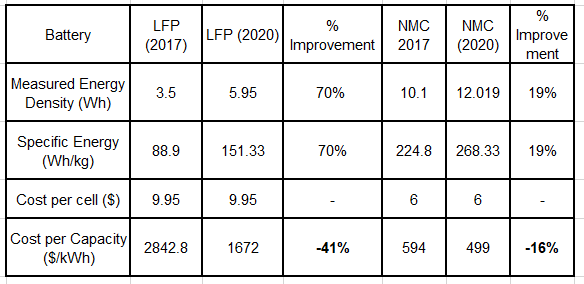
For simplicity, and lack of deep understanding on raw material pricing, I am assuming that cost per cell is the same. This is highly unlikely, but suggests that the cost reduction could be far more substantial.
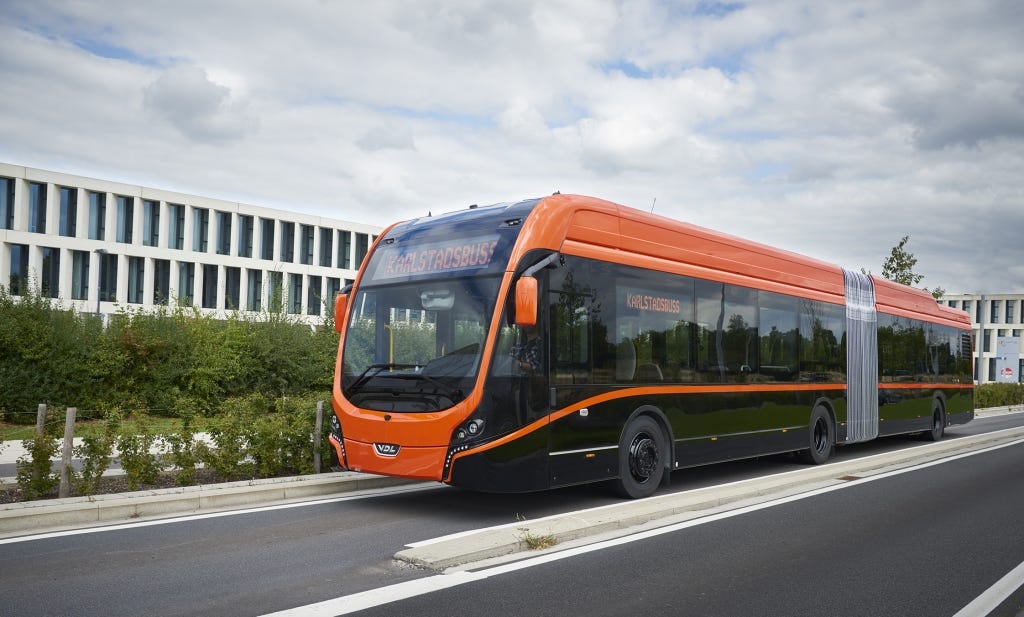
Even more intriguing is the potential for weight reduction using LFP. According to the 2017 data(1), a LFP 18650 cell is roughly 12% lighter than NMC. We are approaching a tipping point. The specific energy of a LFP battery pack is now roughly 56% of the best NMC packs. Therefore, if we do a simplistic comparison to the world’s longest range EVs we have the potential for a LFP powered electric sedan with a range of over 150 miles.
This is getting particularly appealing, because customers that live in cold climates have long had the excuse that their battery would not hold up in the harshest of winters. The operating temperature window of LFP goes down to -30 Celsius, so it is much more stable than NMC.
Quietly LFP could be EV producers’ solution for the masses. Stay tuned for part 3 as I will tie in the potential of LFP, and how I see it shaping the future.
Sources:
“A Database for Comparative Electrochemical Performance of Commercial 18650 -Format Lithium-ion Cells.” H. Barkholtz. Journal of The Electrochemical Society, 164 (12) A2697-A2706 (2017.